"Ji Do Ka" översatt som "self move happen", men de japanska tecknen för jidoka kan även översättas som "self work happen" när man lägger till symbolen för människa i symbolen för jidoka. Båda symbolerna uttalas Jidoka, men automation (self move happen) innebär att något sker av sig självt och autonomation (self work happen) att det inte bara automatiseras utan även utförs ett arbete. "Move" är ju som bekant en Muda (slöseri) och anses således inte vara ett värdeskapande arbete. Med autonomation menade således Taiichi Ohno att man inte bara skulle automatisera, man skulle även bygga in en smartness i processen.
Några av de viktigaste elementen av Jidoka är poka yoke, andon, kamishibai och de närbesläktade metoderna problemlösning och standardiserat arbete. Dessa metoder/mekanismer ämnar att göra vad Ohno ville - automatisera med en "human touch". Poka yoke betyder idiotsäkert och andon betyder signal. Det senare är en signal som maskinen ska avge när det stöter på ett problem den inte själv kan lösa. På det sättet bygger man in intelligens i maskinens utförande och inte bara automatiserar. Poka yoke är enkla mekanismer som ämnar att ta bort möjligheten till att göra fel ur en process. Detta kan exempelvis vara jiggar och fysiska stopp. Ett alldagligt exempel är USB-kontakten som du bara kan sätta i på ett sätt (utan onödigt våld).
Andra metoder som används inom jidoka är fixed position stop, FIFO, 2 in a row, 7QC Tools, Inspektionoch givetvis sekvensen "stop call wait" som blivit revolutionerande populär i tillverkande industrin för sin enkelhet.
I den lite populärkulturella lean-speglingen av TPS (toyota production system) placeras även QC (quality control), QA (quality assurance) och QD (quality design) under Jidoka. Underhållsmetoderna brukar även de hamna i detta fack.
Kvalitet handlar inte om att vända på papper utan att bygga in kvalitet i process och produkt. ISO och QMS (Quality Management Systems) är bra och var hjälpsamt för många år sedan för de företag som inte hade något som helst systematiskt arbete med kvalitet. Idag räcker det dock inte, det krävs ett annat tillvägagångssätt och ett annat tänk.
Jidoka
Lika viktig som JIT, men mindre välkänd, är den andra pelaren av Toyotas produktionssystem - Jidoka. Jidoka betyder autonomation, vilket Toyota brukar förklara som automation med en "human touch". Det är kvalitetssäkringssystemet, som bygger in kvalitet i process och produkt inom Lean.
Inbyggd kvalitet
Det finns tre nivåer av förebyggande för att försäkra oss om att det blir så; Vi kontrollerar och inspekterar produkten eller tjänsten (Quality Control, QC), bygger ut behovet av att inspektera produkten eller tjänsten genom att istället bygga in kvaliten i processen (Quality Assurance, QA) och slutligen så bygger vi in kvaliteten i produkten från början (Quality in Design, QD). QC ger oss feedback så att vi kan göra ett bättre jobb i QA, som i sin tur ger oss feedback att designa smartare i QD. Självändamålet med QC är att göra QA så bra att QC inte behövs. Samma sak gäller för QA. För att stödja det beteende som krävs av organisationen är det viktigt att företaget har en kvalitetsmedvetenhet (Quality Mindset, QM) i alla delar av organisationen.

Quality Control
QC handlar om att hitta och lösa problem. I Toyotas Produktionssystem kikar vi in i Jidoka-pelaren och hittar några av de viktigaste verktygen, typiskt sätt indelat i tre F: Finn, Flagga och Fixa!
Finn handlar först och främst om att ha en tydlig standard för vad som är OK och vad som inte är det. Sedan behövs det en inspektion för att identifiera avvikelsen. Inspektion kan ske i slutet av en process, mitt i processen eller före processens start (e.g., ankomstkontroll). Paradoxalt nog brukar vi vara duktiga på att inspektera våra produkter, dock sämre på att definiera en tydlig standard för vad vi ska inspektera. Speciellt en standard vi delar mellan kunder, oss själva och leverantörer. Lite utav det olyckliga ackord-tänket som lever kvar. Viktiga verktyg och "tänk" här är 2-in-a-row, FIFO, 5S, fixed-position stops, poka yokes ochperformance monitoring. Standardiserat arbete är också mycket centralt, både för medarbetarna i processen som för inspektörerna.
Det andra F:et, Flagga, handlar mycket om vad vi gör när vi hittar ett problem. Även här är visualiseringsverktyg centrala. Andon, Japanska för signal, är det lean-verktyg som används för att skapa eskaleringsprocesser. Här kan vi antingen skapa ett automatiserat system som tänder lampor och spelar musik när ett fel uppstår eller jobba med mer informella andons (t.ex. att du ska ropa på din team leader när ett fel uppstår som du inte hinner fixa själv).
Det tredje F:et, Fixa, består av två saker: Performance management system och Problemlösning. Ett av de viktigaste verktygen för alla företag är att ha en gemensamt problemlösningsmetod. Kvalitet är oftast ägare av metodiken, men det är av största vikt att samtliga delar av organisationen aktivt använder denna metod. Det är ett oerhört tydligt sigill för framgångsrika företag - alla har en egen, inarbetad och rotad problemlösningsmetodik. Detta ger ett gemensamt språk att lösa problem och således även ett gemensamt språk att genomföra förbättringar, eftersom metodiken i stort är detsamma.
QC handlar om de tre F:en. Använder vi dem väl blir det en oerhört bra källa för insamling av information att ge feedback till QA och QD på.
Right first time
Centralt i Lean och nyckel inom Jidoka-tänket är Right First Time (RFT). Både som KPI och tänk. Det ständiga fokuserat att eliminera slöserier manifesterar sig i att göra just Right First Time för att undvika en mängd av slöserier från att ske. Inom RFT finner vi kvalitetsmetoderna inom Lean. I vissa Lean kretsar anser man även att TPM (underhåll) är en del av Jidoka, vilket till viss del är rätt, men vi brukar lägga TPM-delan av Lean under standardisering, delvis då vi tycker den hör hemma där och delvis för att ge ett mer tydligt ansvarsdelande mellan kvalitet- och underhållsavdelningar när vi hjälper företag genomföra transformationer.
Kvalitet kostar dessutom pengar. Mycket pengar. Det är inte onormalt för företag att få tillbaka 1-3% av sina produkter i reklamation. 1-3%! Det är inte heller ovanligt för producerande företag att ha 1 av 10 medarbetare som jobbar med att släcka kvalitetsbränder eller inspektera produkter för att hitta bränderna. 10% av bemanningskostnaden! För tjänsteföretag är det inte onormalt att 1 av 10 spenderar sin tid med kundsupport eller felsökning. Vidare ligger många företag längre bak i värdekedjan med en scrap på 1-5% av sin materialkostnad. Lägger man ihop all bemanningskostnad, lagerkostnad, materialkostnad, transportkostnad, svett och tårar i alla delar av försörjningskedjan så är det nästan konstigt att det inte finns en större marknad av tjänster inom kvalitetsområdet. Total Cost of non-Quality kan ibland vara så hög som 10% av den totala kostnaden för en produkt eller tjänst. 10% av ren waste! Då har vi inte ens nämnt effekten dålig kvalitet kan få ett brand name med tillhörande försäljningssiffror eller till och med ett företags existens.
Vad ska vi då göra? Lean har varit ett populärt sätt att göra kvalitet praktiskt. Six Sigma ett sätt att göra det mer detaljerat och reducera variabilitet ur processer. Vi har försökt sätta ihop ett ramverk som låter oss prata om kvalitet ur flera praktiska perspektiv, både genom olika delar av organisationen och i olika tidpunkter av produktens livscykel. I grund och botten handlar kvalitet om att leverera en produkt eller tjänst som möter kundens förväntan.
Cost of poor quality
Quality Assurance
Allt vi lär oss från vårt QC arbete ska ses som input till vårt QA arbete. Målet med QA är att ta bort behovet av QC genom att bygga om processer, bygga in kvalitet och bygga ut möjlighet till problem. QC är vår direkt nästa kund och vi ska ge dem en fantastisk upplevelse!
Några av de viktigaste verktygen vi har att luta oss på i denna fas är våra processuppbyggnads-dokument;Manufacturing Quality Chart, MQC; Failure Mode and Effect Analysis, FMEA, Material and Information Flow Diagram & Analysis, MIFD & MIFA; Parts Inspection Standard, PIS; Standard work(chart, Combination table, assessment sheet etc), SWX och rätt många fler därtill. Dessa dokument behöver vara levande, så att vi lär oss av verkligheten för att säkra att våra processer kontinuerligt förbättras efter de problem som dyker upp.
Andra viktiga verktyg för QA är mer process-orienterade metoder som vi använder i mål att bygga ut kvaliteten. Processer som PPAP, SQAP, Supplier Management, Supplier Development är alla verktyg för att jobba med leverantörerna och stärka deras processer i mål att inte längre se problemet i den egna produktionen. Här använder vi guidelines för hur vi bygger en process med inbygga förutsättningar för god kvalitet, vi tar hänsyn till begrepp som FIFO, U-formade celler med mot-urs flöde, visuellt styre, gravity feed, Gauge R&R, fixturer,process confirmation, kakuri, kanketsu och alla andra viktiga begrepp. QA handlar inte bara om kvalitet, utan vi tar givetvis även hänsyn till viktiga säkerhets-aspekter i arbete. U-formade cellen tillåter oss ju t.ex. att separera på den ytan där medarbetare jobbar (inuti U:et) och den yta där truckar fyller på material (utanför U:et).
Jidoka lär oss ytterliggare en viktig läxa inom QA; att separera människa och maskin. Genom mekanisering, auto eject, auto transfer och även full automatisering kan vi separera maskinen från människan. Detta leder båda till högre produktivitet men även till en situation där vi utnyttjar styrkor på bästa sätt för att bygga in kvalitet. Maskinen fokuserar på att göra produkter med låg variabilitet och hög förmåga att flagga om en avvikelse uppstår. Människan använder sitt intellekt till att lösa problemet när maskinen har bett om hjälp. Människan kan nu hjälpa flera maskiner att lösa problem samtidigt och fokusera sin tid på att lösa problem istället för att utföra repetetiva övningar.
Vi skulle kunna fortsätta rätt länge med att beskriva hur vi bygger den perfekta processen, men vid där här lager hänger ni nog med på vad vi är ute efter - att bygga en process som stoppar uppkomsten av problem och kontinuerligt lär sig själv att undvika uppkomsten av nya problem. Att göra processen till en enda stor självlärande poka yoke!
Quality in Design
Tänk dig att vi kunde designa en produkt som är så bra att QA och QC inte vore nödvändigt. Det vore rätt fantastiskt. Och egentligen inte så svårt. Men tyvärr finns det kunder med olika behov och säljare som faktiskt förstår vad kunden vill ha. Inte vad vi kvalitetsfolk tycker att de borde ha. Toyotas framgång bygger på ett par fundament i detta område.
För det första har Toyota alltid varit försiktig med ny teknologi. Man har behövt en riktigt bra anledning att gå ifrån något beprövat som fungerar. Detta gör att man helt enkelt har färre "unknowns" att lösa problem med. Färre bränder att släcka. Det tillåter givetvis att fokusera mer resurser på att släcka branden för gott.
Det andra som är signifikant är Toyotas QA networks som har standardiserat precis hur varje del i en bil ska designas för att undvika kvalitetsproblem. på samma sätt har man standardiserat exakt hur en skruv ska dras i en plåt när man utvecklar processen. Den här standardiseringen i design av produkt och process gör att det alltid finns ett bästa nuvarande svar på hur man designar något för att designa in kvalite från början. Med andra ord har man under de senaste 50 åren haft levande FMEA för process, produkt och projekt. Varje liten avvikelse har rapporterats och uppdaterats. Varje ny design ner till varje skruv, baseras på dessa levande FMEA'er. Det gör även att man från första penndrag har en tydlig standard för vad som är OK och inte OK kvalitet.
Det sista Toyota gjort väl är att fokusera på kunden. Kvalitet är trots allt något som varje kund upplever. En Audi upplevs till exempel ha högre kvalitet än en Skoda, trots att båda bilarna byggs av samma företag och till stor del inkluderar samma delar. Skoda Octavia och Audi A4 byggs dessutom på samma linje i samma fabrik i Slovakien (som för övrigt har en sjukt tuff linbana från fabriken till testbanan - om ni någonsin är omkring Bratislava bör ni åka och kika på den!). Det finns dock olika sätt att fokusera på kunden och det viktiga med kvalitet är att möte kundens förväntan. Köper kunden en Audi har han eller hon en högre förväntan på produkten än om han eller hon köpte Skodan. Toyota står för tillförlitlighet. Det har man gjort allt för att få kunden att känna. Därför tog man sig till och med starkare ur krisen med bromsarna än innan krisen.
Givetvis finns det en massa verktyg i denna fas med, det är inte bara levande FMEA. Man brukar räkna hit verktyg som Quality Functional Deployment, QDF; Design for Quality, DfQ; Design for Assembly, DfA; Design Drawing and Critical Assessment, DDCA; Gate Review Process, GRP; Design of Experiements, DoE och så vidare.
Jag vill dock framhäva att det viktigaste verktyget av alla är feedback. Så att FMEA'erna kan bli levande. Skicka ut alla era designers i produktionen och låt dem lära sig vilka problem som kan designas bort från produkt eller process.
Quality mindset
Det viktigaste av allt är dock att organisationen är redo för att jobba med kvalitet. Det behöver finnas ett mindset att vilja göra livet bättre för kunden. Låter kanske konstigt att säga, men så är inte alltid fallet. Oftast behöver vi göra omfattande arbeten med att få in en medvetenhet om att kvalitet är viktigt. Vi behöver förklara vad det är. Utbilda hur vi gör. Träna att göra det. Få ledarna i företaget att vara förbilder för det beteende vi vill se i organisationen. Som med alla andra förändringar kommer även denna uppifrån. Vi behöver en ledning som går längst fram och agerar förebilder. Det brukar inte vara så svårt att motivera dem att göra detta om vi bara visar ur mycket pengar vi förlorar på att inte göra det idag. Viktiga aktiviteter för att främja ett Quality Mindset är utbildning, tvärfunktionell rotation, feedback, styrning och uppföljning och produktkännedom. Vi behöver med andra ord få våran organisation att förstå våra kunder, produkter och processer för att vilja ta mer ansvar för dem. Vi behöver sedan lära dem hur man kan göra det.
Separera människa och maskin
Den andra innebörden av Jidoka är att separera männika och maskin. Genom att följa kvalitetstänket och undvika att fel uppstår, samt i de fall detta händer låta maskinen säga till kan vi undvika att babysitta utrustningar och istället lägga medarbetarnas energi och tid på kreativ problemlösning som tar företaget framåt. För att göra detta följer vi ett par principer.
...
...
Automatiseringsprincipen
tbd
7QC tools
Inom kvalitetsteknik talar man ofta om de 7 Quality Control verktygen, som används för att identifiera och klassificera kvalitet och lite mer specifikt kvalitetsproblem. De är mycket användbara och starkt ihopkopplade med praktiskt problemlösning och sex sigma.







Pareto - Utmärkt verktyg för att prioritera arbetek osv
Histogram - lämpliga vid t.ex. toleransproblem, tekniska avvikelser, Cp och Cpk
Control charts (SPS) - Till de mer avancerade problemen där vi misstänker toleransproblem eller maskinproblem som ett av spåren att undersöka
Regressionsanalys - Oftast bättre än man tror. Bra för att utvärdera påverkande faktorer, som t.ex. maskinhastighet, injektionstryck, temperatur, lufttryck osv
Grafer - Data kan formas på många sätt. Det är viktigt att hantera alla olika typer av grafer för att visa data på det sätt att man ser avvikelse
Fiskben - Fiskbensanalysen är en "cause and effect" analys som hjälper till att identifiera första gradens anledningar till problem på ett strukturerar sätt
Check sheets - Enklaste formen av uppföljning ger massvis med information om vad vi har för problem och kan enkelt sammanställas till någon a de andra verktygen
Andon
Andon betyder signal. I den större meningen är Andon Toyotas system för escalation procedure. Det sätt som problem ska lyftas till rätt instans för beslut eller åtgärd.
Den mer specifika och kända appliceringen av Andon är inom Toyota's fabriker där Andonsystemet är kopplat rakt in till ALC'n (Automatic Line Control - en dator). ALC känner av var varje process på linjen är i sin cykel och om t.ex. en medarbetare inte hunnit dragit åt alla moment han eller hon borde efter 45 sekunder plockar ALC upp detta och skickar upp till en Andontavla som tänder en en gul lampa för den processen. När cykeltiden (egentligen linjens takttid) nått sitt slut och medarbetaren fortfarande inte har dragit alla moment i sin cykel så stannar linjen och den gula färgen byts till röd. Typiskt spelas även en lite melodi när lamporna tänds.
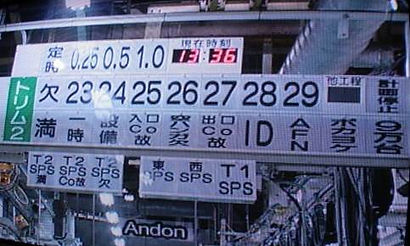
Precis som ALC'n kan flagga ett problem kan givetvis även medarbetaren göra det om han eller hon t.ex. identifierar ett kvalitetsproblem eller någon annan avvikelse. Medarbetare drar då i sitt andon-snöre (hand-on) eller trycker på en lägligt placerad knapp. Andon måste nollställas av team leader för att linjen ska börja snurra (alternativ inte stoppa) igen. Det är ofta magiskt hur mycket en team leader hinner med på de 15-20 sekunder de har på sig att ta sig till processen och lösa problemet innan linjen stoppar.
Andon systemet är en mycket avancerad och dynamisk utrustning som kräver väldigt mycket förarbete. Om du t.ex. har en takt tid på 60 sekunder behöver du så pass standardiserat arbete att du kan säga exakt när varje skruv på din linje ska sättas i för att kontrollera momenten från dessa. Du ska med andra ord inte bara ha det tekniska systemet utan du måste även mapp'a det mot ditt standardiserade arbete. Sedan måste dittstandardiserade arbete följas med minste möjliga avbrott eller variabilitet från dina medarbetare. Annars kommer Andon att slå ut i onödan. Vänder man på steken så är Andon fantastiskt för att förstärka vikten av att ha och följa standardiserat arbete!
Principerna bakom andon är dock viktigare än den fysiska appliceringen. Principerna handlar om att eskalera ett problem för beslut och åtgärd i rätt tid. Detta gör man enklast genom att skapa en s.k. eskaleringsmatris. Eskaleringsmatrisen (se bifogad mall) är ett holistiskt verktyg att applicera på en process eller avdelning där gruppen tillsammans identiferar de problem och risker man ofta stöter på. Sedan definierar man hur och när dessa behöver eskalerar till nästa nivå i organisationen. T.ex. kan man säga att om en medarbetare hittar 2 fel i rad i sin process så ska han eller hon flagga till sin team leader. Många steg senare, när vi inser att det kan finnas en risk att detta når våra kunder behöver någon i organisationen kontakta kunden. Allt detta ska ske inom viss tid från att de första 2 felen upptäcktes. När man gör denna matris så definierar man de lokala andon-principerna och kan sedan friskt fundera kring den fysiska appliceringen av varje princip.
2-in-a-row
2-in-a-row är en enkel kvalitetsprincip som säger att om ett problem uppstår kan du fixa det oh köra vidare men kommer tillexempel två likadana på raken bör du omedelbart stoppa linjen och utreda vad som händer.
2-in-a-row fungerar mycket bra eftersom det är enkelt för den mänskliga hjärnan att köpa konceptet 2 i rad = stopp!
Containment, final inspection och quality corner
Många gånger behövs en sista utpost för att säkerställa att kvalitet är bra innan den når kund. Det finns flera sätt att bygga detta på, men det som anses vara vanligast och effektivast är att ha en 'switchable' flow-out cell som utför en kombination av statistiska kontroller samt 100% inspektion av produkter där det uppmärksammats ett problem eller risk, tills densamma har blivit löst. Under våra problemlösningsakademier där vi hjälper företag med akuta och stora kundproblem sätter vi ofta upp en containment cell för att stoppa problem att nå kund och identiferar sedan problem som vi löser i akademin med mål att kunna ta bort containment cellen igen utan problem till kund. Närbesläktat hittar vi även quality corner.
Ett Quality corner behöver inte nödvändigtvis vara just ett "corner" även om det är lämpligt rent layoutmässigt. Saknar man ett hör går en vägg eller baksidan av några whiteboards lika bra. Syftet med quality corner är att göra kvalitet mer visuellt och självklart på produktionsgolvet. Beroende på fabrikens storlek har man antingen 1 quality corner eller 1 quality corner per avdelning.
I ett quality-corner finns ett par standardkomponenter
-
Aktuella problemlösningar
-
Statistik över kvalitet
-
Boundary samples och inspektionsmetodik (quality board)
Utöver dessa kan ett fritt gäng övriga komponenter ingå lite beroende på vad det är för typ av problem man driver.
Uppföljningsmässigt så träffas man vid tavlorna för rapportering av status på problemlösningen minst 1 gång per vecka. Då rapporterar oftast produktionschefen eller avdelningschefen till kvalitetschef eller VD. Det kan även vara en inköpsperson/chef eller liknande som rapporterar, helt beroende på vem som äger problemlösningen (vilken i sin tur beror på vad det är för typ av problem).
Vi brukar använda quality-corner som ett sätt att bryta mönstret när vi har en kvalitetsavdelning som mestadels pysslar med ISO (dokumentkontroll och miljö..) och få kvalitetsavdelningen och all dess kompetens mer involverad i de verkliga problemen. SAMT få produktion att med hjälp av coaching och struktur lösa surdegarna som legat där ett tag.
Control charts and SPC
Alla processer innehåller variation. Variation kan uppstå i processen av flera olika faktorer som t.ex. maskinkapabilitet, dåligt kalibrerade instrument, luftfuktighet eller till och med sjukdom. Variationen leder ofta till lägre kapacitet eller försämrad kvalitet. Statistisk processtyrning (SPS eller SPC) är ett verktyg för att kontrollera och styra processen med hänsyn till dessa variationer.
Det enklaste, men även mest kraftfulla, sättet att göra SPC är med hjälp av control charts. En control chart är i sin enkelhet ett rutnät med några linjer. Egentligen behövs inte så mycket mer systemkraft en detta. Det som ger control charts kraft är att det är ett levande dokument, som visuellt sitter bredvid maskinen och direkt låter operatören ta beslut efter en tydlig faktagrund.
När vi designar våra control charts så ritar vi in 3 linjer. Först ritar vi in det statistiska medelvärdet för den faktor vi vill mäta och följa. Sedan definierar vi upper & lower control limits - UCL och LCL (+/- 3 standardavvikelser från statistiska medelvärdet). Vi sätter sedan en mätfrekvens som tillåter oss att fånga upp avvikelser innan de blir för digra.
Sedan börjar vi använda control charts och vi tittar då efter två typer a variation i vår graf;
-
Normalvariation (common cause variation). Denna variation finns alltid i processen. Det anses som att man fifflar med processen om man försöker justera denna. Oftast gör det bara situationen värre. Man ska sällan gära något åt normalvariation.
-
Specialvariation (special cause variation). Denna variation skapas av någon abnormal händelse i processen eller processens inputs (se Ishikawa). Typiskt så sätter man regler för att identifiera när detta sker, som t.ex; "mätpunkt ligger utanför någon av UCL eller LCL" eller "8 punkter på raken ligger alla på ena sidan av statistiska medelvärdet"
Control charts är oerhört enkelt, men oerhört kraftfullt och alldeles för bortglömt.

Fixed position stop
Fixed position stop är lika mycket en kvalitetsprincip som det är en infrastrukturell funktion. Lite av en institutionaliserad poka-yoke som ingår inom paraplykonceptet Jidoka. I TPS handbook definieras det enligt utdraget till höger. Fixed position stop är kopplat rakt in i ALC-enheten som styr andon och kommunicerar således direkt med andon-tavlorna när något behöver åtgärdas eller processen gått över tid och plats.
Rent formellt så innebär fixed position stop att antingen om medarbetaren eller ALC ser en avvikelse så aktiveras fixed position stop och produkten kommer stanna när cykeln är slut. Just att den väntar till cykel är slut får många fördelar. Dels så får medarbetaren och team leader en chans att lösa problemet och dels så påverkar det ingen annan förrän deras cykler också är slut (när produkten kommit till fixed position stop stannar hela linjen).
En viktig del i det är att man aldrig ska avsluta en cykel i mitten. Man ska alltid avsluta hela cykeln. Skulle linjen stanna direkt så avbryts alla andra cyklar också mitt i och det kan leda till ökad risk för säkerhets- och kvalitetsproblem.
Fix position stop tillåter oss att effektivt designa pitchen (golvarbetsytan) med hänsyn till 5S, materialförsörjning och standardiserat arbete eftersom fordonet aldrig kommer gå längre än till fixed position stop (och aldrig starta tidigare än fixed position start).


FiFO
Det är många som inte tänker på FIFO (First in First out) som ett kvalitetsverktyg. I själva verket är det ett utomordentligt verktyg för kvalitet då det säkerställer att vi inte har gamla produkter och revisioner i vårt flöde, att kunder får rätt sak i rätt tid, att problem som hittas kan exakt avskärmas till var i flödet de befinner sig etc. Helt enkelt ett mycket viktigt kvalitetsredskap! Innebörden av FIFO i praktiken är att produkter eller tjänster ska produceras i den följd de efterfrågas genom en process utan att byta ordning när de väl startat. Inga delar ska med andra ord 'ligga kvar' eller 'puttas åt sidan'.
Poka yoke

Poka yoke är små mekanismer som ämnar att flagga eller undvika att problem kan uppstå. Dessa smarta mekanismer är hjärtat i process-säkringen och ett av de viktigaste elementen i Jidoka-pelaren i Toyotas produktionssystem.
De nästintill mytomspunna pokayoke-begreppet är både enkelt och oerhört komplicerat. Att hitta några relativt enkla poka yokes för att undvika uppkomsten av ett problem är relativt enkelt. Disketten eller USB-minnet är typiska exempel där det bara går att göra det på ett enkelt sätt. Men att däremot systematiskt förbygga uppkomsten av problem genom att bygga ut dem ur process och framförallt design är betydligt svårare. Har ni till exempel utvecklat en modellprocess för er verksamhet? Hur ser den ut? Har den sådan detaljgrad att den beskriver exakt hur ett moment ska utföras (t.ex. exakt hur en skruv ska skruvas?) Kopplar man ihop poka yoke med sitt proaktiva FMEA arbete (främst på produkt, design och process i detta fall) och konstant återanvänder denna insikt (i Toyotas fall har man gjort det i runt 50 år) för att designa produkter och processer börjar den systematiska appliceringen av poka yoke bli verklighet. Förutsatt att man i sitt proaktiva arbete definierar vilken typ av poka yoke som ska användas och regler för hur den ska fungera bli detta mycket kraftfullt.
De kortsiktiga poka yoke som vi sätter in i processer för att lösa ett specifik problem är givetvis nyttiga och bra, men har man inte tänkt på henkaten kommer man få återupprepa samma poka yoke gång på gång. så systematisk poka yoking är jobbigt med undviker oerhört mycket extra arbete och säkrar processerna från början!
När man designar poka yokes i processer är lösningar med cavities, induktiva sensorer, light beams, fysiska stops/jig och air pressure att föredra då de tar bort möjligheten till fel framför de som bara indikerar att något blivit fel (tänder en lampa om det blev fel). Ett av mina favorit exempel på smart poka yokes är insidan på dörrarna i bilen. Det fanns länge ett problem med att de plast clips man använde för att sätta fast dörrinsidan på plåtdörren ramlade av och blev liggande i dörren. Effekten blev ett rasslande ljud som givetvis inte uppskattades av föraren. Lösningen blev att designa in clipsen i dörrinsidans baksida. Nu fanns det inte längre något risk att clipsen skulle ramla. Det minskade dessutom monteringstiden, claimkostnaden, lagerhanteringen och en hel del andra kostnadstunga delar.
Vi brukar dela i poka yoke i 8 kategorier som är olika lämpade beroende på typ av problem enligt tabell. Tabellen gör det rätt tydligt att det inte finns en "one solution fits all" när det gäller poka yoke, men samtidigt finns det väldigt många poka yoke att testa.
Quality control charts
Kontrollplaner, eller Manufacturing Quality Charts, är själva kärnan eller i alla fall utgångspunkten för kvalitetsarbetet i processerna. Hos Toyota och deras leverantörer är det en mycket viktig nyckel för att bygga in kvalitet. Den bygger oftast på arbete som gjorts när man tog fram sin produkt- och process-FMEA och har sedan gått vidare med att definiera, för varje möjligt kvalitetsfel, var i processen man ska kontrollera, identifiera och säkra denna.
Vi använder oss av två dokument för att skapa våra kontrollplaner, dels en Quality Check Standard Sheet (som vi även utgör ifrån till t.ex. Kamishibai) och dels en Kontrollplan. Ofta bygger vi ihop dessa två filer till ett dokument och kallar det för kvalitetsplan eller helt enkelt även det för kontrollplan. Typiskt sätt gör vi QCSS för en process medan vi gör Kontrollplan för en produkt genom samtliga processer. Således brukar våra kontrollplaner ofta vidarepeka till våra QCSS.
Kontrollplanen hjälper oss genom att definiera var i vårt tillverkningssystem som varje kontroll ska göras samt med QCSS hjälp vilken typ av kontroll som ska göras, hur ofta den ska utföras, vem som ska göra det, o någon som helst fixtur behöver användas och hur mycket tid som gå åt. Denna information är kritisk för att vi ska kunna bygga in kontrollerna i det standardiserade arbetet utan att störa linjebalanseringarna som gjort efteryamazumi-principen.
När vi fyller i våra QCSS finns det ett par saker att ta hänsyn till;
-
Typ av kontroll. Vanligaste typerna av kontroll är visuell inspektion mot standard, mätning med fixtur, dragtest, trycktest, genom känsel, eller i labb
-
Intervall. Här brukar man skilja på första produkten för dagen, för batchen, 100%, 1 gång i veckan eller något intervall där mellan som t.ex. 1/50.
-
Vem ska utföra. Här brukar man välja mellan medarbetare, team leader eller kvalitet
En klassiskt risk när man tar fram dessa dokument första gången är att man har alldeles för många kontroller på alldeles för högt intervall med resultatet att man sölar ner produktion oerhört. Det är därför viktigt att många gånger mjuka i det hela genom att vara lite öppnare i början för att sedan flytta in och skärpa kontrollerna där man ser att det behövs.

Kanketsu
Kanketsu är inbyggd kvalitet genom ägandeskap och ansvar. Principen innebär att en medarbetare kommer identifiera avvikelser bättre i en process om de förstår hela processen och får ett ansvar för den.
Implikationen när vi designar vårt standardiserade arbete är att försöka ge så hela "chunks" av ansvar vi kan till varje delstation så att varje medarbetare avslutar en del. Det är enklare att ta ansvar för att förgasaren är rätt monterad om JAG monterar dit HELA förgasaren istället för att t.ex. jag sätter dit 3 skruvar och en annan medarbetare sätter dit 2 skruvar samt en slang.
Kaikuri
Kakuri är monteringsföljden för att bygga in kvalitet. Enkelt menat innebär det att du inte monterar in ett vasst föremål i bilen innan du sätter i t.ex. sätet - för då ökar du risken att skada sätet på det vassa föremålet.
Henkaten
Henkaten är ett av de viktigaste begreppen i all processorienterat arbete. Henkaten betyder förändringspunkt. Förändringspunkter har vi typiskt mellan olika tidssteg i processer där det vanligaste exemplet kan hittas inom kvalitet;
Vi designar och bygger in kvalitet i en produkt som vi sedan skapar en process till för att bygga in byggkvalitet och till slut installerar kontrollanter för att dagligen se till att allt blev bra. Tre olika processsteg. Quality Design, Quality Assurance och Quality Control. Två Henkaten. Överlämningen mellan QD och QA samt mellan QA och QC.
Varför är då henkaten så centralt?
Det är i henkaten som de allra flesta felen uppstår. Många onödiga slöserier beror på dåligt skött henkaten och många problem kan direkt kopplas tillbaka till aktiviteter som inte fungerar under henkaten. Dessutom är Henkaten även feedbacken som ska se till att problem som uppstår inte återuppstår igen i framtiden. Både i nuvarande processen och för nya produkter. Henkaten management är en av de viktigaste delarna av lean och processförbättringar.
Gage R&R
Gage R&R är ett verktyg för att hantera kvalitetsbedömning. Gage R&R är mycket användningsbart där kvalitetsbedömning inte är helt svartvit. Då kan vi använda Gage R&R för att synk'a så att alla kontrollanter ser samma problem på samma sätt.
Företag med mycket manuell inspektion brukar fira stora segrar med hjälp av Gage R&R, då det hjälper till att både stoppa problem och överkvalitetsproblem. Praktiskt sett innebär det att varje medarbetare för bedöma ett stort urval produkter utefter om de är OK eller inte. När alla medarbetare gör detta kan vi utvärdera flera saker, bland annat;
-
inspekterar vi mot standarder enligt vad våra kunder förväntar sig?
-
Använder alla medarbetare samma kriterium för att skilja OK från NOK?
-
Kan medarbetarna repetera sin egna bedömning eller är det fall till fall?
-
Hur mycket överkvalitet kontra leakage har vi?
-
Vilken utbildningsinsats krävs?
Quality boards
Quality boards (kvalitetstavlor) används för att göra standarder synliga och tydliga. Oftast innehåller en kvalitetstavla tre saker;
-
Limit sample (boundary sample) som så när det är möjligt visar var gränsen mellan OK och NOK går för en produkt så att medarbetare om de är osäkra ska kunna gå till tavlan och jämföra sin produkt mot tavlans
-
Inspektionsrutt, dvs den väg du ska gå med hand och ögon när du inspekterar en produkt. Ofta uppdelat efter olika inspektörer om det finns fler än 1
-
Kontrollmetod och standard för varje område där en kvalitetsstandard är satt
Kvalitetstavlor är ett utmärkt sätt att identifiera nya problemtyper som inte tidigare satts standard för och bestämma dessa. Glöm dock inte att gå tillbaka till design-kvalitetsdokumentationen och uppdatera även där!

Quality measurement system
Ett QMS (inte Quality Management System) är en samling KPIer som används för att följa upp kvaliteten hos ett företag.
Man brukar dela upp uppföljningen av Kvalitet i tre delar, Kund, Process och Leverantör. Egentligen kan samma KPI'er användas på all tre ställen, men det är vanligast att man följer claims, leveransprecision och customer satisfaction index från kunder, PPM och DPM från leverantörer samt Right First Time och PPM internt.
Några av de vanligaste KPI'er som används i QMS är;
CSR, Customer Satisfaction Ratio (Kundnöjdhetsindex)
Ett index som rapporteras månadsvis och inkluderar flera kategorier som t.ex. PPM, DPM, upplevd hantering av problem. Vanligt som kundmått.
COS, Cost of Claims (kan även vara i antal claims)
COS är helt enkelt en månadssammanställning av de kostnader som associerats med claims (produkt, logistik och administrering etc). Vanligt som kundmått.
PPM, Parts Per Million
Vanligaste måttet av kvalitet där man mäter antalet fel per miljon producerade enheter. Som mål har Toyota 15 PPM till hela sin leverantörsbas med undantag bara för castingproducenter. Vanligt som mått både till leverantörer, kunder och egna verksamheten.
DPM, missed Deliveries Per Million
DPM är precis som PPM fast för levererade komponenter. Målet är alltid 0 i en JIT miljö. Vanligt som mått både till leverantörer, kunder och egna verksamheten.
QPR, Quality Problem Report
EN QPR är ett fel så gravt att en rapport varit tvungen att skrivas för det (I Sverige är det vanligt att man skickar en 8D rapport). Antalet QPR som skickas till en leverantör är ett bra mått för att se hur stabila deras processer och organisation är.
repeat QPRs,
Ett ännu bättre mått är repeat QPRs. Ett mått vi verkligen gillar då det sätter fingret på ett företags förmåga att lösa problem.
RFT, Right First Time
RFT är mycket lämpligt mått för den egna verksamheten. Det säger oss hur många av våra produkter som är bra direkt. Oftast är måttet rätt lågt om vi inte har följt det tidigare och vi kan få mycket nytta av att börja mäta det.
OfLV, Off-Line Vehicles
OfLV är ett under-KPI till RFT. OfLV räknar hur många av de fel som dök upp som krävde att vi fick ställa produkten åt sidan för att åtgärda felet.
OnLV, On-Line Vehicles
OnLV är som OfLV med skillnaden att dessa problem lyckas vi åtgärda utan att ta bort produkten från linjen.
DPV, Defect per Vehicle
DPV mäter snittantalet fel per produkt genom antingen en process, en fabrik eller en försörjningskedja. För slutkunden är detta ett bra mått för att se hur väl vi faktiskt byggt in kvalitet i försörjningskedjan
Open Issues
Antalet öppna QPR till exempel. Vi följer antalet öppna issues hos en leverantör, hos oss själva eller mot kund.
Misslabels
En produkt som skickas med fel etikett är ett dubbelt problem. Det är både ett kvalitetsproblem och ett leveransproblem. Dessa väljer vi ibland att flagga med ett eget KPI
Kamishibai
Kamishibai betyder ungefär "bildberättelse" och byggs upp av de tre japanska kanjerna för bild, story och show. Inom Toyotas Produktionssystem används Kamishibai för att planera, visualisera och genomföra audits. Även audits berättar ju en historia och kamishibai ger oss snabbt en översikt i hur det går medan historian berättas.
Även om kamishibai audits används inom flera områden så är de vanligaste tillämpningarna kring underhåll och kvalitet. Kamishibai är centralt för ett företags övergripande control plans (eller manufacturing quality charts) där kamishibai täcker upp och säkrar så att inte alla kontrollpunkter behöver kontrolleras 100% hela tiden. Kamishibai innebär att man tar alla de kontrollpunkter som behöver utföras vid en inspektion eller audit och skriver ner dem på ett antal små kort. Sedan visualiserar man dessa kort på en tavla och linjeledaren/auditören tar ett kort varje tidsenhet (oftast timme, dag eller t.ex. var 50:e produkt) och utför (se exempel på bild ovan). Det är viktigt att man har sådant intervall att man alltid kan stoppa ett problem innan det lämnar fabriken, varför vi ofta föredrar ett per-enhet intervall. Genom att göra dessa kontroller med lägre frekvens avlastar man operatören utan att riskera kvaliteten.
Process för att utforma kamishibai och bygga in det i Andon
Det vi kommer beskriva nu finns det inte många som exakt förstår sig på hur det fungerar. Man måste ha jobbat med det i en Toyota-fabrik för att veta om att det i huvud taget finns. Vi har gjort det och kan därför beskriva hur det fungerar. Vi definierar det på samma sätt oavsett om vi ska ta fram underhållsplanerna eller kvalitetsplanerna. Många gånger gör vi dem ihop som en och samma kamishibai. Vi ska kolla på ett av de många sätt som Toyota bygger in kvalitet i sin process och vi ska studera en steg-för-steg process i hur man definierar och bygger upp en kamishibai samt hur det hänger ihop med Andon.




Steg 1. Definiera kontrollpunkter
För en process, eller linje, ska vi börja med att samla de som är kunniga om kontroller som behöver göras. Detta bör minst vara representanter från produktion, kvalitet & R&D. Plocka fram ett Quality Check Standard Sheet (QCSS, se mall längst ner) och enas om vilka kontrollpunkter som ska ingå. Förhoppningsvis har ni redan en ifylld QCSS (eller liknande) annars har i lite mer arbete att göra här. Har ni redan en ifylld QCSS behöver ni gå igenom och se om alla kontrollpunkter är relevanta samt undersöka senaste månadernas kvalitetsresultat och se om det är någon ny kontroll som borde läggas till. Ni kan läsa mer om hur man fyller i QCSS genom att lösa omkontrollplaner.
Steg 2. Bestäm kontrollintervall
När vi har bestämd vilka kontrollpunkter som ska vara med behöver vi bygga ut dem med lite mer information. Vi behöver säga när de ska kontrolleras;
-
Första produkten av varje batch/dag/skift
-
Kvantitetscheck 1/50
-
LÃ¥gfrekvenscheck 1/300
Vem som ska kontrollera dem;
-
Medarbetare
-
Teamledare
-
Chef
För att skapa en enkel och effektiv process sätter vi två typer av kontrollintervall baserat på antalet enheter. Ett kort och ett lite längre. Sedan försöker vi dela in alla våra kontrollpunkter efter dessa intervall. Som exempel kan vi sätta 1/50 för kvantitetscheckar och 1/300 på lågfrekvenscheckar (1/50 innebär kontroll på ar 50:e produkt). De kontrollpunkter som ska göras på första produkter kan vi antingen lyfta ut ur kamishibai och in i en checklista för första produkten eller både lyfta ut och ha kvar. Oftast lyfter vi ut dem för att undvika dubbelarbete.
Steg 3. Definiera tid per kontroll
Nästa steg är att räkna ut hur lång tid varje kontrollpunkt tar, samt eventuellt om någon form av verktyg krävs. Nu borde hela vår datalista vara klar och vi är redo för lite kamishibai'ande.
Steg 4. Förbered kamishibai-kort
Börja med att dela in alla lågfrekvenskort i en Quality Checking Matrix Chart (QCMC, bild till höger men även denna finns som mall på slutet av sidan). I vårt exempel, där vi har 1/50 och 1/300 intervall, behöver vi ha våra lågfrekvenskontroller på 6 kort. När vi sedan delar upp alla kontrollpunkterna på korten är det viktigt att korten har ungefär lika lång kontrolltid så att vi skapar balans mellan korten (och för kontrollanten). Det är mindre viktigt att få balans på lågfrekvenskontrollerna. Tänk även på tiden att gå mellan kontroller. Om det första kortet tar 60 minuter och det andra 30 minuter kommer vi inte kunna uppfylla standardiserat arbete för cellen. I detta fall behöver vi planera om korten.
När vi är nöjda med vår uppdelning är det dags att skriva varje kort. Korten kan se rätt olika ut beroende på er verksamhet. Ibland är de laminerat A6-format (dubbelvikt A4) och ibland sådana där snygga stämpelklockekort som sitter i ännu snyggare stämpelklockekortshållare (för övrigt en av de enda inredningsdetaljer jag och min fru kommit överens om att vi borde ha hemma - jag vill dock ha dem tillsammans med en stämpelklocka, vilket hon motsäger sig). Jag har även blivit imponerad av magnetkort på whiteboard. Till höger ser ni en bild på de delar som måste finnas med på kortet oavsett hur de ser ut. Det ska finnas;
-
Kortnummer
-
Sekvens av kontrollpunkter (vilka punkter ska utföras, i vilken ordning). Ibland är "ett kort" faktiskt en ihopsättning av instruktioner för alla de kontrollpunkter som ska göras med en enkel förlaga till som beskriver kamishibai-informationen
-
lågfrekvenskontroller. För de kort som är lågfrekvenskontroller skriver vi vilken lågfrevens-checknummer det är, vad som ska kollas samt eventuellt fixturnummer

Steg 5. Säkra risker
Om det finns en risk att processen kan skicka en dålig produkt med vårt intervall (1/50) så ska vi ta bort den processen från kamishibai och istället hantera den genom en räknare med startpunkt. Detta kan ofta vara fallet med t.ex. den sista maskincellen i en tillverkningsenhet, eftersom det inte finns någon station efter den som kan säkerhetsbuffra tiden mellan kontroller innan produkterna skickas till monteringslinjen. Det kan även vara så att processen har haft stabilitetsproblem eller liknande och av den anledningen är under extra lupp med en räknare.
Steg 6. Bygg in i Andon
Ställ in startpunkt för kamishibaisnurran genom att koppla den till den första multiräknaren i en produktionsenhet (typiskt sätt en räknare på den första relevanta maskinen i vår kamishibailoop). I många fall har man inte en så pass stabil verksamhet som Toyota och då kan det vara bättre att koppla kamishibai till flaskhalsen i varje enhet. När vi hittar en räknare att koppla vår kamishibai till ska vi se till att koppla ihop den med vår Andon. Det typiska sättet att göra detta på är att koppla så att;
-
Gul lampa (på Andontavlans högra del) tänds på processen efter 45 produkt-räkningar för att indikera att Kamishibai nu måste utföras (ska även tändas en Q-lampa för att inte förväxla med tool change over)
-
Röd lampa tänds efter 50 räkningar för att indikera att ingen har kvitterat (och således utfört kamishibai). Nu stannar processen till kamishibai är utfört och kvitterat
Nu har vi kopplat ihop vår kamishibai med Andon, så nu är det bara att köra så att det ryker och stanna om problem dyker upp. Den sekvens som kontrollanten nu ska följa är;
-
Gul lampa lyser för andon
-
Plocka upp ett kort från övre högra hörnet av kamishibaitavlan och lämna din namnskylt som indikation på att du nu är ute på kamishibai-äventyr
-
Utför de kvantitativa och lågfrekvenscheckar som finns på ditt kort
-
Återvänd med kortet
-
Skriv datum, tid att utföra och ditt namn på kontrollbladet
-
Ta tillbaka din namnskylt
Det finns några få, men väldigt viktiga regler när vi utför kamishibai
-
När en person utför kamishibai ska de inte utföra någonting annat
-
Ingen talar med eller stör en person som gör kamishibai
-
Samma person ska inte kontinuerligt utföra samma checkarna
-
Om du är osäker, stanna maskinen och fråga efter omdöme från team leader
Kamishibai ingår i flera av våra träningspaket. Läs mer om dem i vår utbildningskatalog.